Moving From Lessons Learned to Concrete Project Improvement Actions
A Fast Method to Generate Insights That Can Lead to Improvements
It happens too often. A capital project is completed and it is accepted that there were missteps that should have been avoided. Figuring out how and where the missteps occurred could result in substantial cost savings on future projects, but getting key business executives and project professionals together to recognize how the right sets of project data and insights can be leveraged to drive major work improvements is a challenge in and of itself.
Many companies use performance metrics and lessons learned to improve their project performance, but in many cases its focus on the engineering function precludes companies from identifying the value of contributions of business, operations and other support functions. IPA has been conducting the Team Lessons Learned Workshop (TLLW) for clients for more than a decade to facilitate lesson learned endeavors. Such workshops have been conducted for the oil and gas; refining; mining, minerals processing, and metals; and chemical industries for projects with values ranging from $15 million to over several billion. The workshop’s objective is to examine a project organization’s performance on individual projects and glean clear insights for use in developing and implementing lessons learned.
“The workshops are most effective when conducted in conjunction with project closeouts.”
TLLWs are most effective when they are conducted in conjunction with or shortly after project closeouts. A closeout evaluation provides highly valuable industry context and findings, including the project’s performance metrics and industry data. Together they integrate relevant team experiences and a wealth of insights from over 600 research studies we have completed during the last 25 years.
For instance, a project team may contend it achieved excellent cost performance because of a 20 percent underrun on a project it delivered. But IPA’s cost analysis of the same project could end up showing that the actual project cost was actually 15 percent higher than industry average—certainly not a cost competitive project. Such context is essential in convincing company executives to act on lessons learned to preserve capital project value during development and execution.
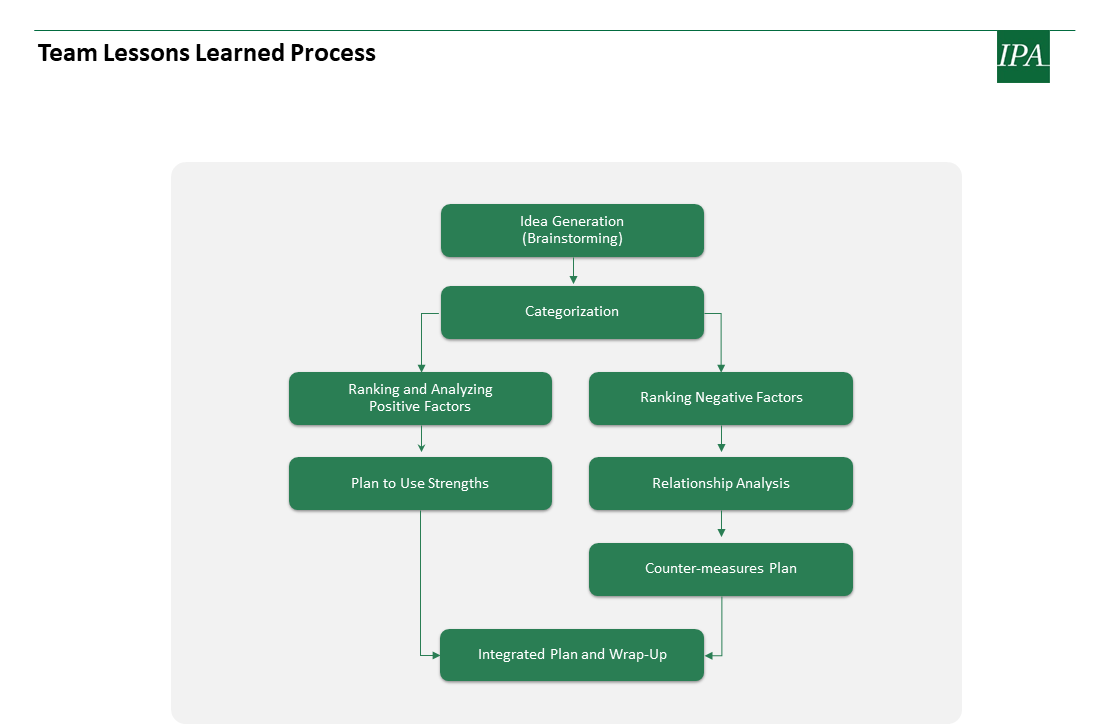
Figure 1
Figure 1 shows a basic outline of how a typical TLLW works. The TLLW is used to generate lessons by rapidly processing the factors that contributed to the project outcomes. The positive and negative factors are developed by grouping the positive and negative (areas of improvement) ideas generated during a brainstorming session. We process positive and negative factors separately leading to a discussion with senior management about an improvement plan that integrates lessons from positive factors and countermeasures of negative factors.
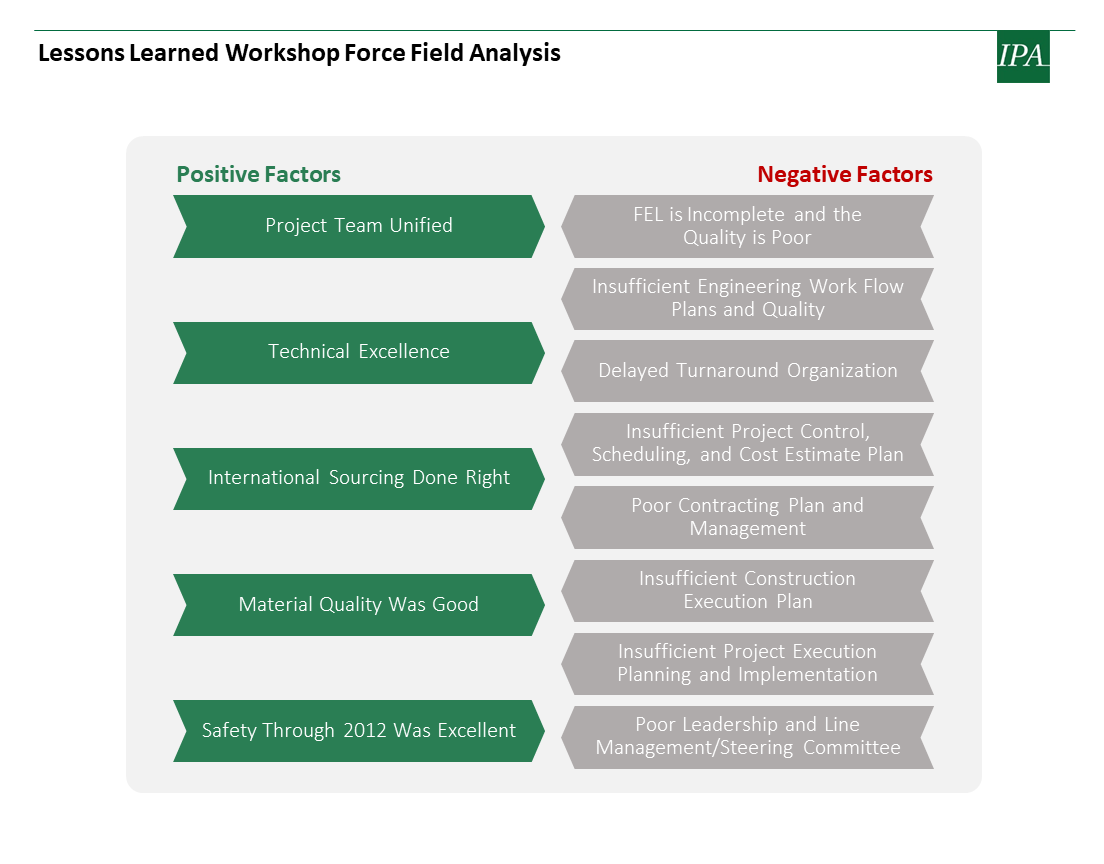
Figure 2
TLLW findings on positive and negative factors are summarized in a force field analysis graph, as shown in Figure 2. The positive factors are analyzed and a plan to use these project strengths is developed. The negative factors are analyzed based on their effect on the projects and interdependencies.
As shown in Figure 3, interdependencies among all categorized negative factors are illustrated as red circles. The arrows illustrate the causal relationship among all, as assessed by the project team members during the session. The boxes next to the circles describe the number of arrows departing (OUT) and arriving (IN) for each factor. The factors with more OUT arrows are influential drivers of performance; the factors with more IN arrows (but fewer OUT factors) are less significant.
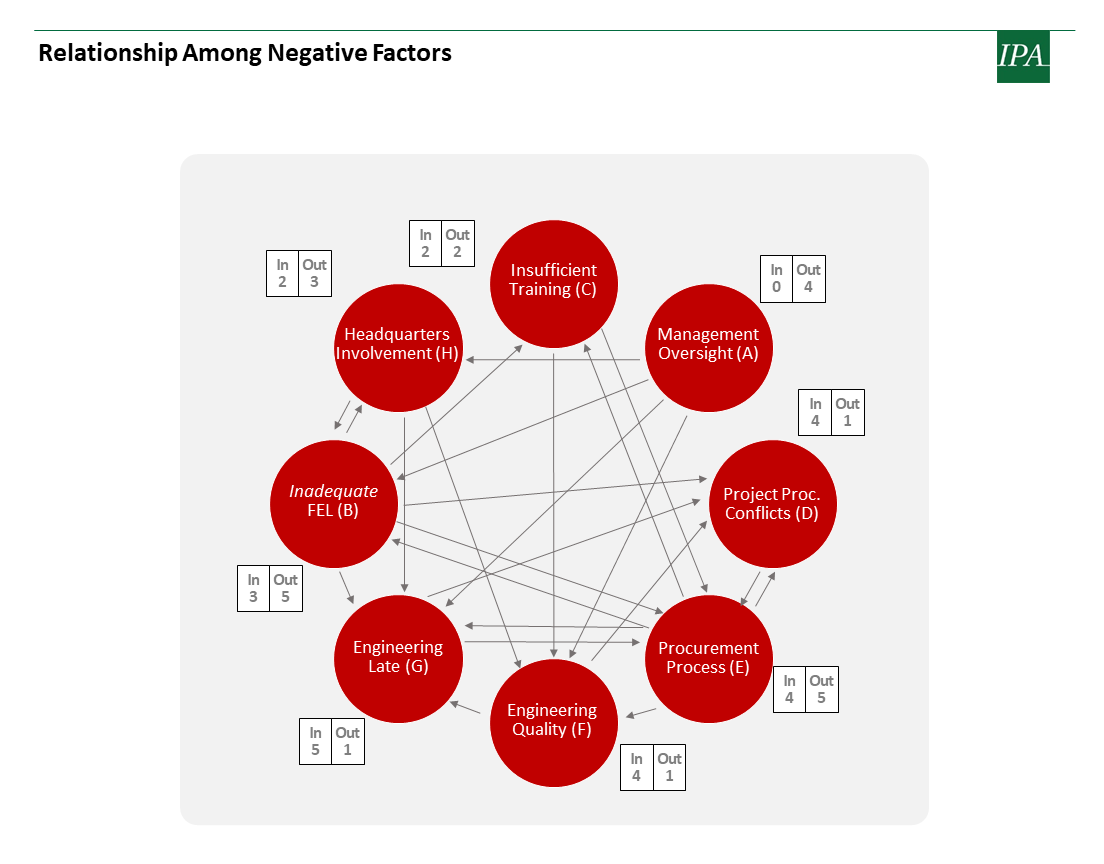
Figure 3
The interrelationship digraph shown in Figure 3 can provide insights and context to reveal root causes of performance problems and develop implementation plans. The aim is to understand and eliminate the most influential drivers of poor performance. When combined with ratings about the effect on these factors on the project, root causes as well as “low hanging fruits” for improvement are developed as part of the countermeasures plan.
It is very likely that some of the key learnings relate to systemic issues, but it may not be clear how frequent those issues are encountered in other projects, so management’s perspective is important. Thus, a wrap-up or follow-up sessions with senior management is held to focus on what went well and important root causes of project performance such as decision making, project framing and shaping, the stage-gated process, how the project system works on a daily basis, and the plan for implementing the action plan. Senior management leadership is essential to translate the lessons into action plans that can be implemented. In many cases, management realizes that their actions during the business planning phase (e.g., FEL 1) are major drivers of project success.
“Root causes as well as “low hanging fruits” for improvement are developed as part of the countermeasures plan.”
It is important to note that business sponsorship for the TLLW must be cognizant that collaboration with senior management is essential to drive the changes required to achieve major performance improvements. All too often lessons learned are given low priority or the project management organization owns the process, but does not have the authority to make changes to the work process. In most cases this opportunity is missed because the role of operations business, and project sponsor have not been defined for the project systems or FEL 1 phase.
The TLLW is a very fast method to generate lessons learned that can lead to concrete improvement plans. The facilitated sessions allow the team members to share their experiences, identify strengths, root causes, and translate system issues into an improvement plan that can be discussed and led by senior management. Importantly, when combined with a Closeout Evaluation, senior management can also use a wealth of quantitative benchmarking data and lessons from thousands of capital projects to improve company’s capital project productivity.